Ceramic Band Heaters, Knuckle Band Heaters-Construction
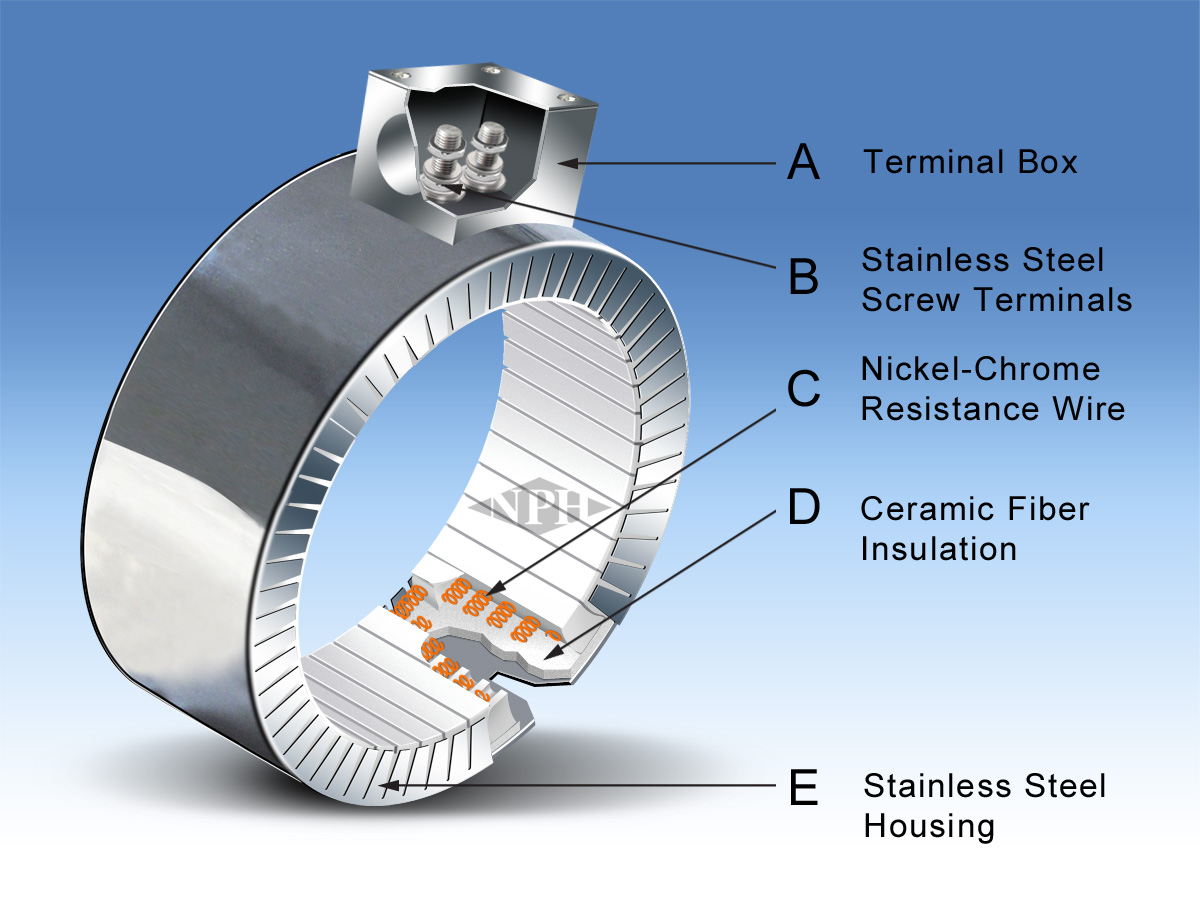
Ceramic Band Heaters, Knuckle Band Heaters-Construction
- Nickel Chromium Heating Coil
- Insulation
- Housing
- Termination
Heating Coil- The helically wound heating coil is the actual resistance which is where the electrical load occurs. The most common type of metal alloy used for this purpose is a Nickel-Chromium mixture, also known as Nichrome. The Nichrome wire is wound around a ceramic core, and the number of spirals per inch vary according to the requested watt density. Potential from an alternating current source, which can either be 2 phase or 3 phase, flows through the coiled Nichrome wire, heating up the wire, which in turn, heats the cartridge heater sheath.
Insulation- Built in ceramic fiber insulation is used to prevent the Nichrome coil to contact the sheath. If such event happened, it would ground the resistance and produce a catastrophic short-circuit, resulting in a melted sheath and a major equipment failure. To prevent the coil from touching the sheath, the coil is strung through custom designed ceramic insulating bricks.
Stainless Steel Housing- The housing is the part of the ceramic band heater which holds the ceramic knuckles inside the band together. Several metal alloys are used, for the housing. The most common types of housings are made from stainless steel or stainless steel alloy.
Termination- Since ceramic band heaters are installed in a wide variety of machines, manufacturers must design the heaters to meet certain clearances. The knuckle band heaters might be terminated with terminal box with screw terminals and or leads coming out straight, or in a right angle. Also, manufacturer must be careful that the leads are not exposed to temperatures higher than the maximum rating for the lead wire. In order to prevent lead wire damage from temperature, movement or contamination, the lead wire can be protected with metal conduit or braided metal.
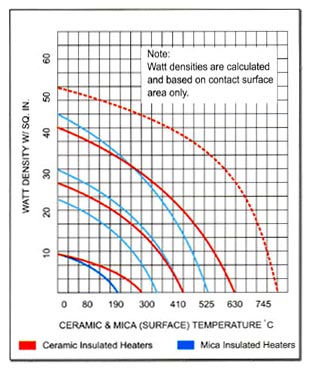
Advantages of Ceramic Knuckle Band Heaters:
- Lower Operating Cost-Because of superior insulation, less heat escapes to the air and less wattage is required to? maintain barrel temperature. Ceramic Fiber Insulation reduces power consumption by 20 to 30%. See comparison heat loss chart below.
- Safety- Also the heater is safer because the external surface is much cooler.
- Operator Comfort- With the majority of the heat going directly to your process, the ceramic band heater gives off significantly less heat to ambient air than a mica band heater.
- Longer Heater Life- because all materials used are rated to operate at very high temperatures.
- Higher Operating Temperatures
- Flexible- easy to install and remove
- Dual Heat Transfer- Heat is transferred through both radiation and conduction so a near perfect fit is not required as with other heaters, such as mica heaters.
COMPARISON OF INSULATED VERSUS NON-INSULATED
BANDS IN TERMS OF WASTED ENERGY
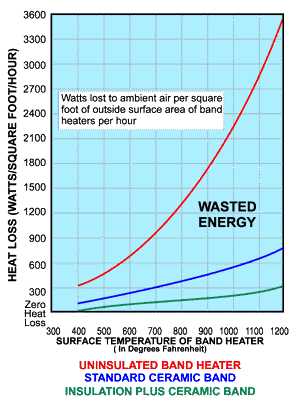
- Nickel Chromium Heating Coil
- Insulation
- Housing
- Termination
Heating Coil- The helically wound heating coil is the actual resistance which is where the electrical load occurs. The most common type of metal alloy used for this purpose is a Nickel-Chromium mixture, also known as Nichrome. The Nichrome wire is wound around a ceramic core, and the number of spirals per inch vary according to the requested watt density. Potential from an alternating current source, which can either be 2 phase or 3 phase, flows through the coiled Nichrome wire, heating up the wire, which in turn, heats the cartridge heater sheath.
Insulation- Built in ceramic fiber insulation is used to prevent the Nichrome coil to contact the sheath. If such event happened, it would ground the resistance and produce a catastrophic short-circuit, resulting in a melted sheath and a major equipment failure. To prevent the coil from touching the sheath, the coil is strung through custom designed ceramic insulating bricks.
Stainless Steel Housing- The housing is the part of the ceramic band heater which holds the ceramic knuckles inside the band together. Several metal alloys are used, for the housing.� The most common types of housings are made from stainless steel or stainless steel alloy.
Termination- Since ceramic band heaters are installed in a wide variety of machines, manufacturers must design the heaters to meet certain clearances. The knuckle band heaters might be terminated with terminal box with screw terminals and or leads coming out straight, or in a right angle. Also, manufacturer must be careful that the leads are not exposed to temperatures higher than the maximum rating for the lead wire. In order to prevent lead wire damage from temperature, movement or contamination, the lead wire can be protected with metal conduit or braided metal.
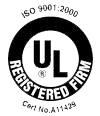
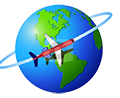
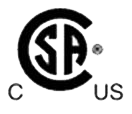
We Ship Our Kapton & Process Heaters To OEM’s & Industry World Wide