Ceramic Infrared Panels, Platens and Controls
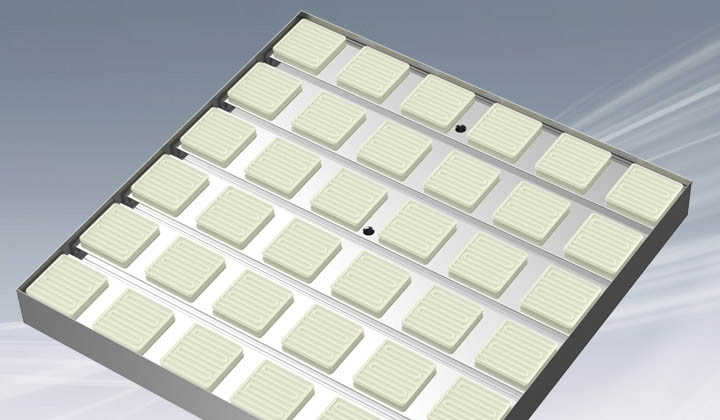
Ceramic Infrared Panels/Platens and Ovens
Thermoforming, Platens and Control
Ceramic infrared heaters make thermoforming profitable
The plastics thermoforming industry is often accused of being energy intensive and inaccurate compared to plastics injection moulding but NPH industrial heat consultants now have the expertise and partners to supply infrared replacement heaters for thermoforming to thousands of thermoformers worldwide – saving the industry millions and improving thermoforming line efficiency in the process.
Specializing in reducing costs for thermoforming a simple upgrade to an infrared heating system can increase the user's profit margin by up to 40%. The infrared heating upgrade is designed to improve the performance of a fixed capital asset that would take millions to replace and the upgrade typically pays for itself within months.'
In addition, for a very low five figure sum a sophisticated upgrade to a fixed and expensive capital asset can be supplied and not only pay for itself within months but also make you 40% more money on the output which you were having to make anyway. Not only that but the move will significantly prolong the life of your fixed machinery.'
Infrared heating in thermoforming produces a host of other benefits, including:
- Major reduction in capital equipment wear and tear
- Like-for-like infrared for tubular replacements
- Elimination of ‘hot box' tubular problems
- No need for changes in control or instrumentation
- Poor performing infrared to be replaced with superior platens
- Savings in directional heat
- Better resultant product quality
- Improved set up time and tool change time
- More complex parts possible
- Cooling requirements also reduced
- Matching of heating control systems to polymers being processed
- Improved environment for operators
Our view is that many thermoforming companies spend their time unnecessarily fretting about raising the capital for an expensive new machine. The reality is that a heating upgrade can make them more money now.
Custom and Standard Ceramic Infrared Panels:
Usually made from 20 Ga. [.36" (.9mm)] polished aluminized steel with one or more terminal blocks and mounting studs. Custom infrared panels or ovens can be fitted with either FTE, FFE, HTE, HFE ceramic emitters and mounted in any direction.
A complete refector assembly with reflector, outer case, terminal blocks and a red pilot light. The units are prewired and suitable for applications operating in free air at 70F (21 C). The PAS-1-PAS-5 has a mounting system that is easily adjustable to change the angle/direcction it is facing.
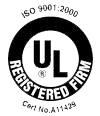
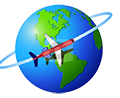
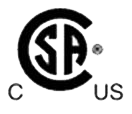
We Ship Our Kapton & Process Heaters To OEM’s & Industry World Wide