Review & Buy Split Sheath Cartridge Heaters
Expanding Split Sheath Cartridge Heaters
Common Issues with Standard Cartridge Heaters:
Heater removal: a cartridge heater will oxidize after many hours of operation and maybe difficult to remove. Consider drilling a through hole so the heater can be hammered out or choosea split sheath cartridge heater.
Lubricantslike graphite or silicone facilitate the insertion of the cartridge heater but can carbonize at higher temperature and then the heater will be really stuck.
For process temperatures above 450 deg F, use high- temp lead wire and ceramic bead insulation. Or order the heater with an additional length of cold section.
The location of the temperature sensor is very critical. If the sensor is too far from the heater, then the surrounding area's ability to dissipate the heat generated by the heater may be exceeded.
The NPHsplit sheath cartridge heateris designed especially for platen, die or mold industrial heating applications where the holes are poorly drilled or worn through age. Independent expansion of each section of the split sheath cartridge heater when energized, creates intimate contact with the wall of the hole.
Through the patented split-sheath design and highly specialized manufacturing techniques, NPH split sheath insertion heatersreduce your total cost of process heating by an average of 40% over other heaters.
NPH's split sheath cartridge heaters use a unique, patented split-sheath design that expand when energized to maximize heat transfer through greater contact with the wall of the bore.Better heat transfermeansless poweris consumed to maintain the set point temperature, reducing operating costs.
This heater construction eliminates ceramic cores typically found in conventional cartridge heaters. NPH has developed and highly-specialized manufacturing techniques to compacthigh-grade MgO dielectricto its near theoretical maximum around the heater coil, which increases dielectric strength and heat transfer away from the coil which results insignificantly longer heater life.
Split sheath cartridge heaterslast up to 5 times longerthan conventional heaters withless downtimefor heater replacements andlower maintenancecosts. NPH split sheath cartridge heaters contract when de-energized, eliminating bore seizure and the need for expensive drill-outs.
Lubricantslike graphite or silicone facilitate the insertion of the cartridge heater but can carbonize at higher temperature and then the heater will be really stuck.
For process temperatures above 450 deg F, use high- temp lead wire and ceramic bead insulation. Or order the heater with an additional length of cold section.
The location of the temperature sensor is very critical. If the sensor is too far from the heater, then the surrounding area's ability to dissipate the heat generated by the heater may be exceeded.
The NPHsplit sheath cartridge heateris designed especially for platen, die or mold industrial heating applications where the holes are poorly drilled or worn through age. Independent expansion of each section of the split sheath cartridge heater when energized, creates intimate contact with the wall of the hole.
Through the patented split-sheath design and highly specialized manufacturing techniques, NPH split sheath insertion heatersreduce your total cost of process heating by an average of 40% over other heaters.
NPH's split sheath cartridge heaters use a unique, patented split-sheath design that expand when energized to maximize heat transfer through greater contact with the wall of the bore.Better heat transfermeansless poweris consumed to maintain the set point temperature, reducing operating costs.
This heater construction eliminates ceramic cores typically found in conventional cartridge heaters. NPH has developed and highly-specialized manufacturing techniques to compacthigh-grade MgO dielectricto its near theoretical maximum around the heater coil, which increases dielectric strength and heat transfer away from the coil which results insignificantly longer heater life.
Split sheath cartridge heaterslast up to 5 times longerthan conventional heaters withless downtimefor heater replacements andlower maintenancecosts. NPH split sheath cartridge heaters contract when de-energized, eliminating bore seizure and the need for expensive drill-outs.
Maximize Heat Transfer
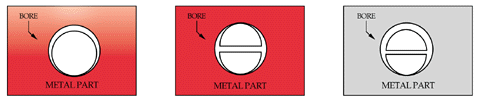
Conventional Cartridge Heater-Energized
NPH Split Sheath Heater Energized
NPH De-Energized Cartridge Heater
Conventional Cartridge: is limited to ordinary thermal expansion, cannot compensate for oversized bores.
NPH Split Sheath Energized Heater: The unique bi-lateral expansion of an energized NPH split sheath cartridge heater produces superior metal-to-metal contact with the surrounding bore, thereby maximizing heat transfer.
NPH Cartridge Heater De-Energized: When de-energized, the NPH split sheath cartridge heater contracts for easy removal from bore.
Split Sheath Cartridge Heaters Selection Guide:The key questions which need to be answered before selecting a cartridge heater for your application are:
- How much wattage is required?
- What voltage will be used?
- What is the heated length? What is the overall length?
- How long are the heater leads or what is the lead length required?
- What is the dimentions of the cartridge heater?
- What is the ambient temperature the cartridge heater will see?
- What is the maximum temperature required from the heater?
- How quickly do you want to reach your operating temperature or set point in hour/minutes?
- What is the type and weight (in lbs.) of the material you want to heat?
- Special Modifications
How To Order Cartridge Heaters




We Ship Our Kapton & Process Heaters To OEM’s & Industry World Wide